What Is Drawing?
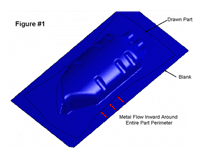
Figure 1
Drawing is a metal forming process in which a product is made by
controlling sheet metal flow into a cavity and over a punch. The
process of deep drawing means that the part must be taller than its
minimum width.
Many people confuse drawing with stretching. True drawing results in
very little stretching of the metal. Drawing requires metal flow, while
stretching does not. It is only through the drawing process that
objects such as oil pans, beer kegs, and oil filters can be made.
Drawing can be better defined as the process of displacing
pre-existing surface into an alternate-shaped vessel containing nearly
the same surface area. Stretching can be defined as the increase of
surface area that results in a product with more surface area than the
original surface area.
Drawing requires the metal to feed inward toward the punch. Very
little or no metal flow takes place during stretching. However, keep in
mind that because drawing does require tension to pull the metal
inward, some stretching occurs during drawing.
The key in deep drawing is to limit the amount of metal stretching
and thinning that take place. Items such as oil pans require
significant drawing and stretching. Achieving a deep-drawn product that
exhibits very little metal thinning requires extensive knowledge of
sheet metal properties, drawing ratios, radii, and friction.Figure 1 shows the drawing process.
Basic Drawing Components

Figure 2
the deep-drawing process is not directional-specific. in other
words, the direction in which the drawing takes place really doesn't
matter. you can draw a part up or down into a cavity. you can even draw
a part vertically using cams or special vertical-motion presses.
please keep in mind that i am in no way indicating that process
engineers or die designers don't pay close attention to the direction
in which are drawing. drawing direction must be given careful attention
because it affects the ability to move, cut, and eject the part in the
die. if drawing is incorporated into a progressive die, the drawing
direction also may affect the die and strip carrier
design.
Figure 2 shows a section view of a very simple
single-action drawing die. this die is designed to produce a round cup
with a small flange. a basic drawing die consists of the following
components:
1. Die set or foundation. This could be made of
mild steel cast iron or aluminum. It serves as the guided foundation on
which all of the metal forming sections will be mounted.
2. Draw cavity. The draw cavity represents the
drawing die's female portion. Uually made from tool steel or solid
carbide, it serves as the cavity in which the metal is formed.
3. Ejectors and knockouts. These pressure-loaded
components serve to push or eject the part from the draw cavity. a
high-pressure knockout must be timed properly so that it pushes the
part out of the cavity after the die has fully separated. If the
knockout is timed incorrectly, the part can be crushed during the
return stroke of the press.
An alternate method to using a knockout is to use a small ejector
pin and a lightweight spring. this spring must have enough force to
eject the part adequately but not deform it during the press's return
stroke. The pin and spring method does not require specific timing.
However, keep in mind that certain part geometries require a great deal
of force to eject from the cavity. in such cases, a
timed high-pressure knockout may be necessary.
4. Air vents. Air can be trapped during drawing.
This trapped air must be vented out of the tool. Not venting the air
can cause defective parts, splitting, and wrinkling, as well as make it
difficult to strip the drawn part from the cavity.
It is critical that both the cavity and punch contain air vents. Air
vents in the cavity allow trapped air to escape during the downstroke
of the press; air vents in the punch allow air to be pulled into the
punch, which prevents suction during the part-stripping process.
5. Die face. The die face is the surface
surrounding the cavity. it can be a flat or a contoured surface. this
surface interfaces with the sheet metal and keeps it from wrinkling
during the drawing process. the die face typically is made of tool
steel or carbide and is highly polished in the direction of metal flow.
6. Draw punch. This component represents the male
shape of the drawn part geometry. Like the cavity, it usually is made
of tool steel. In most cases, it is polished to a mirrorlike surface.
However, there are times when a rough surface is desired.

Figure 3
7. Blank holder /draw pad / binder. This
pressure-loaded plate, which serves to keep the metal from wrinkling
during the drawing process, typically is loaded with gas springs.
However, certain drawing dies can achieve the force needed to control
metal flow through the use of a press cushion.
8. Pressure system. The pressure system supplies
the force necessary to control metal flow. It may consist of gas, coil,
hydraulic, or urethane springs. Certain drawing dies utilize a press
cushion to obtain the needed pressure. A press cushion is a plate or
series of vertically moving thick, flat plates mounted beneath the
press's bolster plate. These plates transfer the
force to the bottom of the draw pad using a cushion pin (Figure 3).
9. Equalizer block. This block functions to
maintain a specific gap between the die face and the draw pad surface.
It also allows for minor adjustments to be made with respect to how
much pressure is being applied to the blank.